From Design to Dispatch: A Deep Dive into the Backpack Manufacturing Process
The humble backpack – a ubiquitous companion in our daily lives. Whether slung over the shoulder of a student navigating campus, strapped to the back of a hiker conquering trails, or carried by a professional commuting to work, backpacks are essential for carrying our belongings comfortably and efficiently. But have you ever paused to consider the intricate journey a backpack undertakes before it reaches our hands? The seemingly simple bag is, in fact, the product of a complex manufacturing process involving design ingenuity, material selection, skilled craftsmanship, and rigorous quality control.
This article will embark on a detailed exploration of the backpack manufacturing process, unraveling the steps involved in transforming raw materials into the functional and fashionable backpacks we rely on every day. From initial design concepts to final dispatch, we will examine each stage, highlighting the technologies, techniques, and human expertise that contribute to the creation of these essential accessories.
Phase 1: Design and Planning – Conceptualizing Functionality and Style
The journey of a backpack begins not on the factory floor, but in the design studio. This phase is crucial, laying the groundwork for the entire manufacturing process. Designers must consider a multitude of factors, blending functionality, aesthetics, and manufacturability.
-
Conceptualization and Needs Assessment: The design process begins with a clear understanding of the backpack’s intended purpose. Is it for school, hiking, travel, or a specific niche activity? Target users, anticipated load capacity, desired features (like water resistance, laptop compartments, or hydration systems), and style preferences are all meticulously considered. Market research and trend analysis inform design direction, ensuring the backpack meets consumer demands and aesthetic trends.
-
Sketching and 3D Modeling: Designers translate initial concepts into sketches, exploring various shapes, sizes, pocket configurations, and aesthetic elements. Traditional sketching might be combined with Computer-Aided Design (CAD) software to create detailed 3D models. These digital prototypes allow for precise visualization, ergonomic testing, and virtual simulations to assess functionality and aesthetics before physical production begins.
-
Pattern Making and Prototyping: Once a design is finalized in the digital realm, pattern making begins. This involves creating 2D templates for each component of the backpack – main panels, side panels, pockets, straps, flaps, and reinforcement pieces. Patterns are typically created digitally and can be printed or cut using automated systems. Prototypes are then meticulously hand-sewn using sample materials. This crucial step allows designers to evaluate the design in physical form, identify any fit issues, refine patterns, and test the backpack’s functionality and construction. Multiple prototypes may be created and iterated upon before a design is deemed production-ready.
-
Material Selection: Parallel to design development, material selection is a critical process. Backpacks require a variety of materials, each chosen for specific properties:
- Outer Fabric: Durable, abrasion-resistant, water-resistant or waterproof fabrics like polyester, nylon, canvas, or Cordura® are common choices. Factors like denier (fabric thickness) and weave pattern influence durability and texture.
- Lining Fabric: Lighter-weight fabrics like polyester or nylon are used for lining, providing internal structure, water resistance, and a finished interior.
- Webbing and Straps: Strong nylon or polyester webbing is used for straps, handles, and reinforcement binding. Webbing width, thickness, and weave pattern are chosen based on load-bearing requirements and comfort.
- Padding Materials: Foam padding (closed-cell or open-cell) is crucial for shoulder straps, back panels, and hip belts, providing cushioning and comfort. Density and thickness of padding are varied based on load and intended use.
- Zippers and Fasteners: Durable zippers (nylon coil or metal), buckles, snaps, and Velcro® closures are selected for their reliability and longevity. Quality zippers are essential for backpack functionality.
- Reinforcement Materials: For high-stress areas, materials like reinforced webbing, bar-tack stitching, and durable threads are chosen to enhance structural integrity.
Phase 2: Material Procurement and Preparation – Setting the Stage for Production
Related articles 01:
1. https://hami.vn/chon-balo-cho-con-vao-lop-1-dau-tu-cho-suc-khoe-va-niem-vui-den-truong/
4. https://hami.vn/the-rise-of-recycled-backpacks-sustainable-style-and-functional-design/
5. https://hami.vn/the-backbone-of-your-carry-exploring-the-diverse-materials-behind-backpacks-in-2025/
With designs finalized and materials specified, the manufacturing process moves to procurement and preparation, ensuring a smooth and efficient production flow.
-
Material Sourcing and Quality Control: Raw materials are sourced from suppliers, often globally. Fabric rolls, webbing spools, zippers, buckles, and padding sheets are procured in bulk. Incoming materials undergo rigorous quality control checks to ensure they meet specified standards for color consistency, fabric weight, tensile strength, water resistance, and zipper/buckle functionality. Materials that fail quality checks are rejected, maintaining product quality.
-
Fabric Cutting – Precision and Efficiency: Fabric rolls are laid out in multiple layers (layering) on large cutting tables to maximize cutting efficiency. Precise cutting is crucial for backpack construction, and various methods are employed:
- Die-Cutting: For high-volume production of basic shapes, die-cutting uses sharp metal dies to stamp out fabric pieces accurately and rapidly.
- Laser Cutting: Computer-controlled laser cutters offer high precision and flexibility for intricate shapes and patterns. Laser cutting is particularly useful for technical backpacks with complex designs.
- Automated Blade Cutting: Computer-controlled blade cutters offer a balance of speed and precision, suitable for various fabric types and complex patterns.
- Manual Cutting: For smaller production runs or intricate prototypes, skilled cutters use hand-held rotary cutters or shears to cut fabric pieces following patterns, ensuring accuracy.
-
Component Preparation: Beyond fabric cutting, other components undergo preparation:
- Strap and Webbing Cutting: Webbing rolls are cut to specified lengths for straps, handles, and reinforcement binding using automated cutters.
- Padding Shaping: Foam padding is cut or molded to specific shapes for shoulder straps, back panels, and hip belts.
- Zipper and Fastener Preparation: Zipper lengths are cut, zipper sliders are attached, and buckle and snap components are sorted for assembly.
- Printing and Embellishment: If designs include logos, labels, or decorative prints, these are applied to fabric panels before sewing, using techniques like screen printing, heat transfer, or embroidery.
Phase 3: Sewing and Assembly – Bringing the Backpack to Life
The sewing and assembly phase is where individual fabric pieces, components, and hardware are skillfully joined together to create the final backpack form.
-
Panel Sewing and Sub-Assembly: Sewing operators, often using specialized industrial sewing machines, begin assembling backpack components. This includes:
- Pocket Attachment: Pockets are sewn onto main panels, reinforcing stitching is applied at stress points, and zipper or Velcro® closures are attached.
- Panel Joining: Side panels, bottom panels, and top panels are joined to the main front and back panels, forming the basic backpack body. Seam types (flat-felled, bound seams) are chosen for strength and water resistance.
- Strap and Handle Construction: Shoulder straps are sewn, padding inserts are placed, and adjustable webbing straps and buckles are attached. Handles are constructed and reinforced for carrying strength.
- Internal Organization: Internal dividers, laptop sleeves, pen holders, and other organizational compartments are sewn into the lining panels, which are then assembled into the backpack interior.
-
Main Assembly and Reinforcement: Once sub-assemblies are complete, the main backpack body is assembled:
- Lining Insertion: The prepared lining is carefully inserted and sewn into the outer shell of the backpack, creating a clean interior finish and adding structural integrity.
- Strap and Handle Attachment: Shoulder straps and handles are securely sewn onto the backpack body, with multiple rows of stitching and bar-tack reinforcement at stress points to withstand heavy loads.
- Zipper and Closure Installation: Main zippers, pocket zippers, and any Velcro® or snap closures are meticulously sewn and tested for smooth operation.
- Hardware Attachment: Buckles, clips, adjusters, D-rings, and other hardware components are riveted, stitched, or securely attached to designated points on the backpack.
-
Specialized Sewing Techniques: Backpack manufacturing often utilizes specialized sewing techniques for durability and weather resistance:
- Reinforcement Stitching: Bar-tack stitching, box stitching, and triple stitching are used at stress points (strap attachment points, handle bases, zipper ends) to prevent tearing and ensure long-lasting durability.
- Water-Resistant Seam Sealing: For waterproof or water-resistant backpacks, seams may be taped or sealed with specialized tapes or coatings to prevent water penetration.
- Binding and Edge Finishing: Raw fabric edges are often bound with webbing or fabric tape to prevent fraying and create a clean, finished appearance.
Phase 4: Quality Control and Finishing – Ensuring a Premium Product
Related articles 02:
2. https://hami.vn/backpack-blunders-common-mistakes-to-avoid-when-choosing-your-carry-all/
3. https://hami.vn/gieo-mam-tuong-lai-tam-quan-trong-cua-viec-cho-tre-hoc-ngoai-ngu-som/
4. https://hami.vn/the-rise-of-recycled-backpacks-sustainable-style-and-functional-design/
5. https://hami.vn/stitching-the-future-the-state-of-the-apparel-industry-in-2025/
Quality control is an integral part of backpack manufacturing, ensuring that each backpack meets rigorous standards for durability, functionality, and aesthetics.
-
In-Process Inspections: Quality checks are performed throughout the sewing and assembly process. Inspectors examine cut pieces for accuracy, check seam quality, verify proper hardware attachment, and identify any defects in workmanship at each stage of production.
-
Final Inspection and Testing: Finished backpacks undergo a comprehensive final inspection. This includes:
- Visual Inspection: Checking for cosmetic defects, loose threads, misaligned seams, zipper flaws, and overall aesthetic appearance.
- Functionality Testing: Testing zipper and buckle operation, strap adjustability, load-bearing capacity (using weighted tests), and water resistance (using spray tests or submersion tests for waterproof backpacks).
- Dimensional Checks: Verifying that backpack dimensions and pocket sizes meet specifications using measuring tools and templates.
-
Finishing and Packaging: Backpacks that pass final inspection proceed to finishing and packaging:
- Thread Trimming and Cleaning: Loose threads are trimmed, and any fabric marks or smudges are cleaned to ensure a pristine appearance.
- Final Hardware Check and Adjustment: Buckles and straps are adjusted to their loosest settings for packaging and display.
- Folding and Packaging: Backpacks are carefully folded or shaped and placed in individual poly bags or packaging materials. Retail packaging may include hang tags, labels, and promotional materials.
- Boxing and Dispatch: Packaged backpacks are placed in cartons for shipping and dispatched to distribution centers, retailers, or directly to consumers.
Sustainability and Ethical Considerations in Backpack Manufacturing
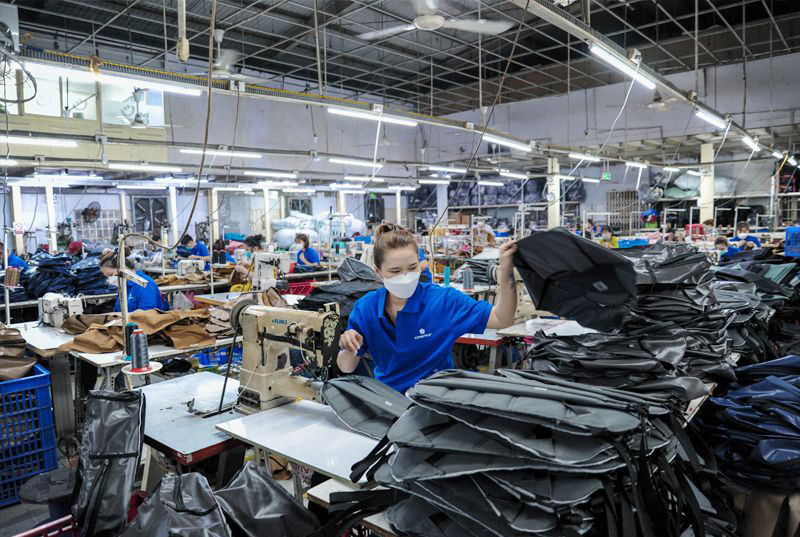
Modern backpack manufacturing increasingly emphasizes sustainability and ethical production practices.
- Eco-Friendly Materials: Manufacturers are exploring and adopting sustainable materials like recycled polyester (rPET) made from recycled plastic bottles, organic cotton, and plant-based alternatives to traditional nylon.
- Ethical Labor Practices: Brands and manufacturers are increasingly focusing on fair labor practices, ensuring safe working conditions, fair wages, and compliance with labor laws in their factories. Certifications like Fair Trade and SA8000 are increasingly sought after.
- Waste Reduction and Recycling: Efforts to reduce fabric waste during cutting, recycle fabric scraps, and minimize packaging waste are becoming more prevalent in the industry.
- Durable and Long-Lasting Products: Producing high-quality, durable backpacks designed for longevity is itself a form of sustainability, reducing the need for frequent replacements and minimizing overall consumption.
Conclusion: A Symphony of Skill and Precision
The journey of a backpack from initial concept to finished product is a testament to the complex and multifaceted nature of modern manufacturing. It involves a symphony of design ingenuity, material science, precision engineering, skilled craftsmanship, and rigorous quality control. From the designer’s vision to the sewing operator’s deft hands, countless individuals and processes contribute to creating the backpacks we rely on daily. The next time you reach for your trusty backpack, take a moment to appreciate the intricate process and dedication that went into its creation – a process that seamlessly blends functionality, style, and durability into a seemingly simple yet essential everyday item.